Corrosion Protection Coatings
For corrosion resistant coatings, the DECC Company utilizes both barrier and sacrificial types of engineered coatings. These coatings adhere to the metal substrate and provide added protection against salt, chemicals, and high-temperature corrosive environments.
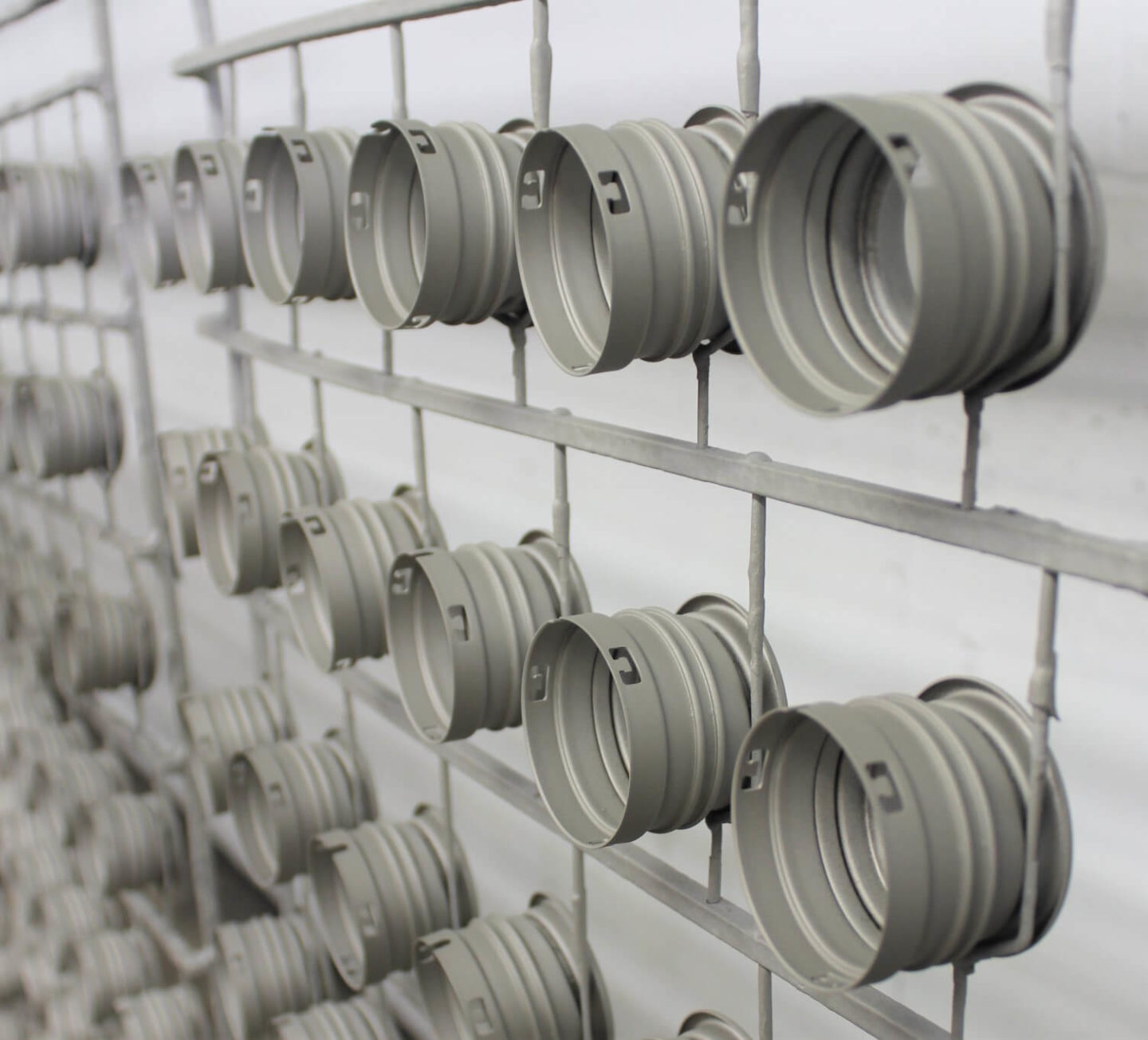
Benefits of Corrosion Resistant Coatings
Fuel Economy
Increases fuel economy when applied to certain automotive parts
Lubricates
Lubricates parts which reduce load caused by friction
Functionality
Improves functionality with a longer part life cycle
Resistance
Resists harsh chemicals and extreme temperatures
Cost Savings
Lowers cost of servicing requirements as parts last longer
Corrosion Resistant Barrier Coatings
Barrier coatings provide a consistent film that prevents external elements from penetrating to the substrate. In other words, a barrier coating utilizes a thin layer of plastic resin which acts as a shield that blocks external factors from causing harm to the part. Every barrier coating contains a plastic resin protection layer which then combines with a filler layer to solve a specific problem. Wall paint, for instance, uses a coloring additive mixed with plastic resin and would be considered a barrier coating as it provides protection for the drywall while providing cosmetic appeal.
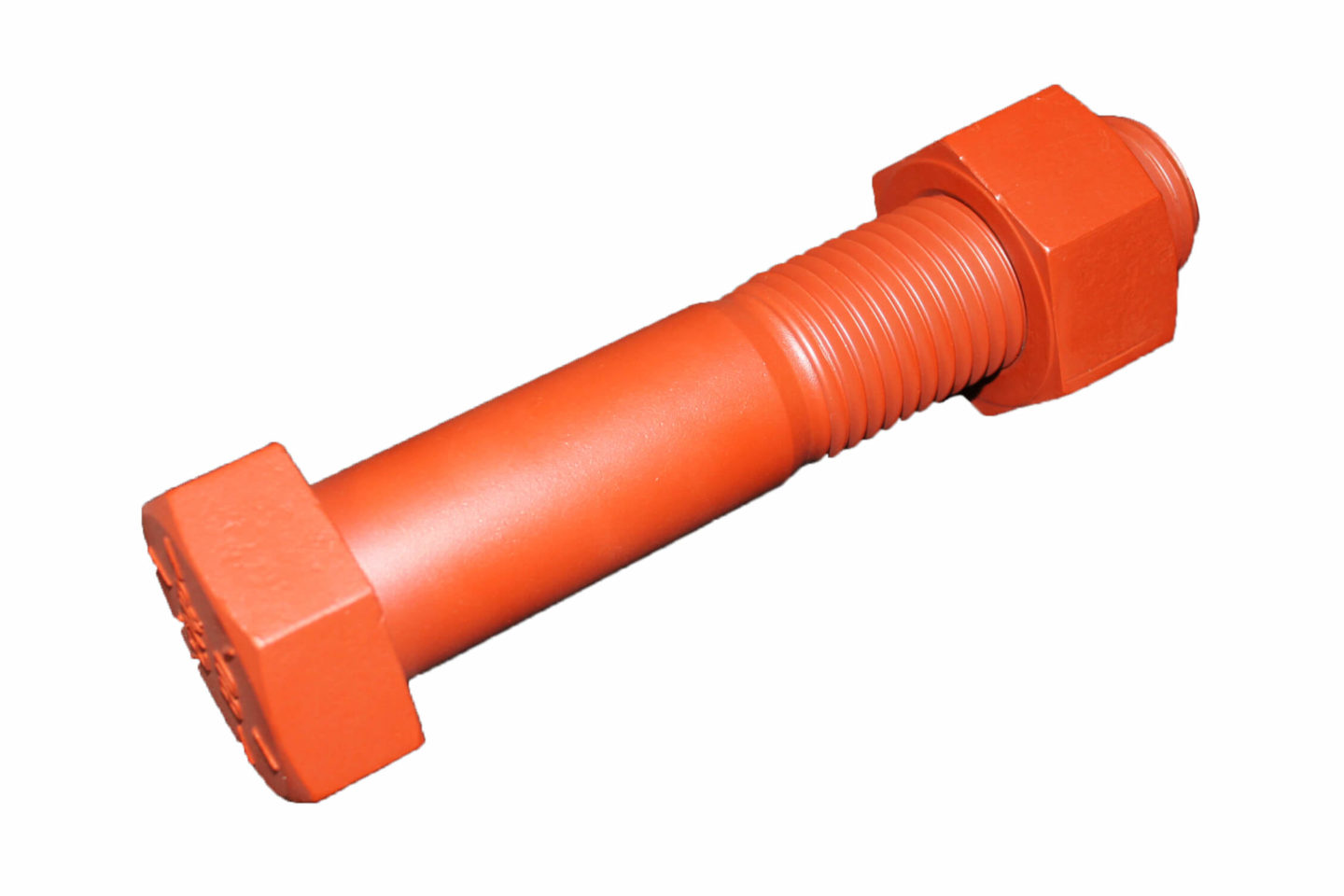
Corrosion Resistant Sacrificial Coatings
Sacrificial coatings contain certain elements, such as aluminum or zinc, which oxidize sacrificially to ensure that the substrate remains corrosion free. The salt spray resistant coatings, some which meet up to 1000+ hours of resistance, can also prevent galvanic corrosion when dissimilar metals are in contact with each other. Sacrificial coatings essentially fool the rust into eating away at the coating instead of the metal layers beneath. This happens because aluminum, or in some cases zinc, is added to the epoxy resin during the coating’s manufacturing process.
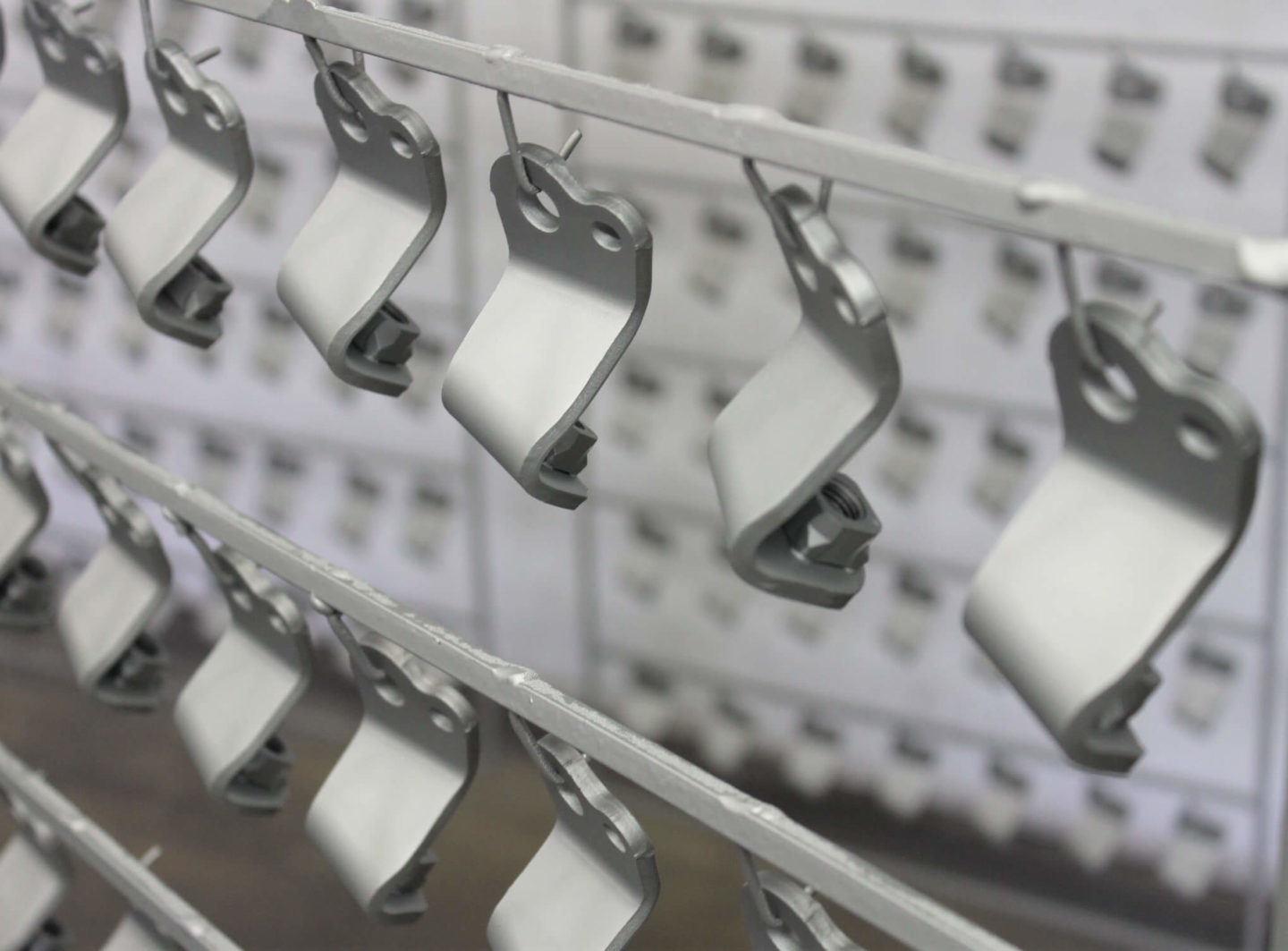
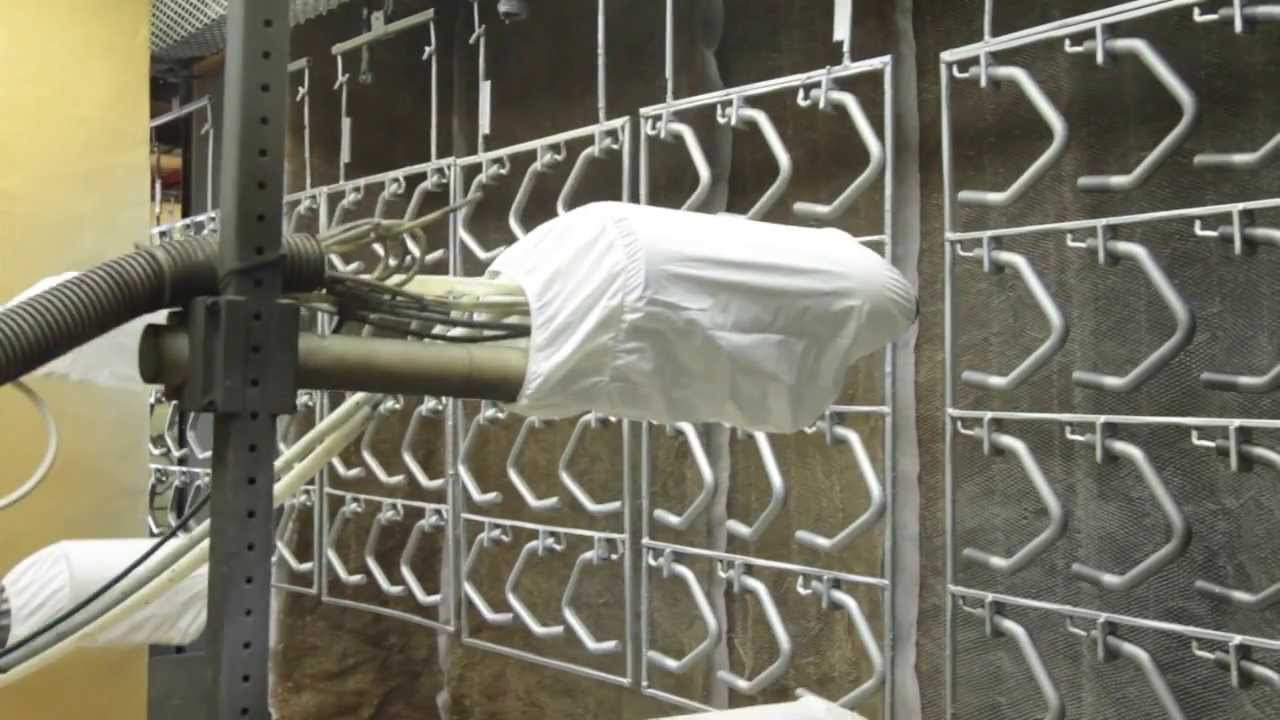
Coating Products for Corrosion Protection
For over 50 years, DECC has worked hard to supply our customers with the most reliable protective coating application options. We strive to deliver solutions for each of our customer’s unique needs, regardless of the difficulty of the challenge presented.
The DECC Company is fully equipped and ready to solve your problem with an effective, low-cost solution.
Acheson
The Emralon 310, Molydag 250 and Molydag 254 lubricants all provide corrosion resistance for a variety of components.
Doerken
All Doerken coatings are designed to combat corrosion.
Dow Corning
The majority of the Molykote line provides outstanding corrosion protection.
Lord Corporation
Chemlok 6254 is a DECC preferred coating that is used for the rubber-to-metal bonding process and is corrosion resistant, as well. We also use Chemlok 6260 for similar projects.
The Magni Group
DECC is a Magni-approved applicator. All of the Magni coatings have been designed specifically to protect components from corrosion.
Whitford
DECC is a Whitford-approved applicator. Many Xylan coatings are designed with corrosion protection as a top priority.
Types of Corrosion
Atmospheric Corrosion
This term is used to describe any of a range of corrosive causes that may be present in an indoor or outdoor atmosphere. Multiple factors may work together to cause atmospheric corrosion. ISO 9223 standards rank environmental corrosiveness from C1 (least aggressive) to CX (most aggressive). This classification can help determine what materials may or may not be suitable for the application and environment, but atmospheric corrosion can occur even if material precautions are taken. Surface conditions can increase atmospheric corrosion-coarse surfaces tend to collect dirt and other particulates that can ultimately lead to corrosion, whereas smooth surfaces are less susceptible.
Crevice Corrosion
Formed in tight spaces where oxygen content is limited, crevice corrosion generally affects flanges, threaded connections, and other mechanical joints in equipment and machinery. Dissolved metal ions and chloride ions infiltrate these low-oxygen crevices, creating large, shallow areas of corrosion.
Carburization
Certain metals and alloys may become carburized in high-temperature environments where carbon monoxide, carbon dioxide, methane, or other hydrocarbon gases are present. The effects of carburization can vary greatly depending on the amount of carbon and oxygen in the atmosphere, the working temperature, and the composition of the metal. In addition to external corrosion, carburization can also cause embrittlement and, in extreme cases, the disintegration of the material, leading to severe pits and holes.
Galvanic Corrosion
In any potentially corrosive environment where two dissimilar metals come into repeated mechanical contact, galvanic corrosion is likely to take place. Materials such as carbon and galvanized steel, copper, and brass are all highly susceptible to this destructive process. In galvanic corrosion, the metal with lower positive electrode potential is generally more affected, and corrosion rates can be very high and fast-acting. Both barrier and sacrificial coatings from the DECC Company provide effective solutions for galvanic corrosion.
High-Temperature Corrosion
High-temperature atmospheres rich in oxygen, sulfur, or halogens can cause severe corrosive reactions. These "reducing" environments can affect aluminum, silicon, chromium, and other metals and alloys. Special high-temperature coatings from DECC can protect most metallic substrates against corrosive reactions at elevated temperatures.
Intergranular Corrosion
Though modern metals, with lowered carbon contents, are generally immune to intergranular corrosion, it is still a risk for any material containing carbon. The instigating factor in intergranular corrosion is high temperatures above 1,000°F (550°C). Heat treating metals is an excellent way to prevent this type of corrosion; the DECC Company offers a range of thermal barrier coatings to protect non-heat treated materials.
Oxidation
Generally referred to as rusting, oxidation occurs when Iron is exposed to oxygen in the environment, and therefore is perhaps the most common form of corrosion. Temperature variations can accelerate the oxidation process. Rust scales made of iron oxide develop on the surface, which can somewhat paradoxically provide protection against further oxidation. However, rust can also penetrate deep into metal materials. There are a number of methods of preventing oxidation, from simply painting the surface to DECC's specialized corrosion resistant coatings.
Pitting Corrosion
Generally highly localized, pitting corrosion causes discrete pits on unprotected metal surfaces. Each pit effects a very small surface area, but the corrosion rate is high and often fast-acting. There are a number of potential causes of pitting corrosion, including seawater exposure, high-chloride process solutions, oxidative chemicals, and more. All of these factors can be exacerbated by increased temperatures and low-pH environments.
Sulfidation
Sulfidation is similar to oxidation but is caused by exposure to sulfur compounds in process gases rather than oxygen. Nickel alloys are particularly susceptible to sulfidation and can experience rapid deterioration. Sulfide scales, similar to rust scales, often form, but these do not provide the protection that oxide scales do. DECC applies a phenolic resin system to diesel components to combat this very issue.
Uniform Corrosion
As the name suggests, uniform corrosion is consistent degradation across a large part of an unprotected metal surface, often the entire surface. Uniform corrosion generally occurs in work environments with constant temperature and chemical exposure, and generally takes place at a constant, if gradual, rate. It is usually easier to protect against than localized corrosion processes.
Cracking & Fatigue
Though not technically corrosion, cracking and fatigue are still very harmful to metal and alloy materials. Generally caused by a combination of mechanical stress and corrosive environmental factors, cracking can spread very quickly and cause more rapid failure than corrosion alone. Corrosion fatigue is usually caused by a combination of cyclic load and corrosive factors, and can quickly lower the material's fatigue strength. A corrosion resistant coating from DECC will help combat the corrosive factors that lead to undue cracking and fatigue.
Related Articles
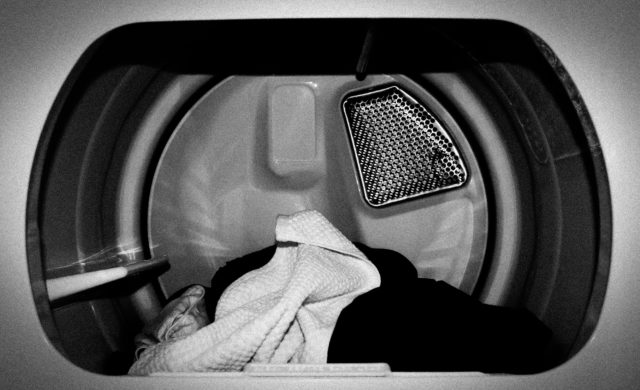
Reduce Plastic Sticking with Dryer Panel Coatings
DECC SOLVES PROBLEM OF PLASTIC STICKING TO DRYER PANELS
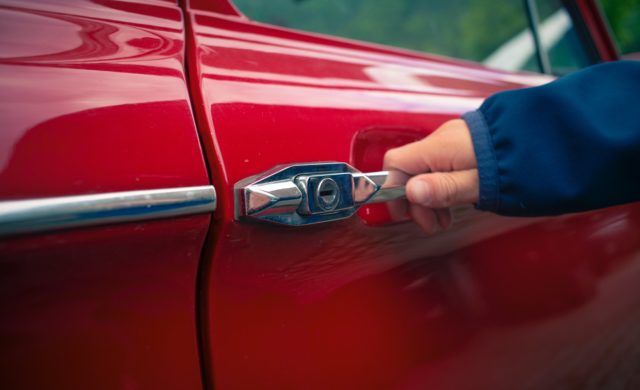
Coatings for a Quiet Ride
As cars have gotten quieter and quieter over the years, auto makers have...
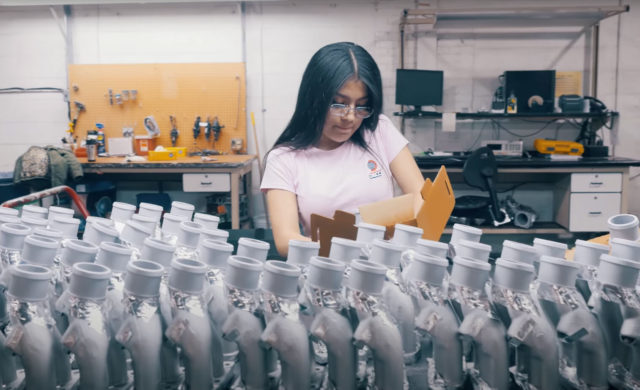
Dip Spin vs. Rack Spray – Why Not Both?
When it comes to the application of liquid-based functional coatings, there are two...