Cyclic Corrosion Testing 101
In the past several years, Cyclic Corrosion Testing, or CCT, has become a common practice in the automotive industry.
Designed to accelerate corrosion in a laboratory environment, CCT tests how materials used in the auto sector will react to the weather, stimuli, and conditions encountered on the road.This, in turn, allows manufacturers to prepare their materials accordingly, contributing to the longevity and durability of modern automobiles.
What is Cyclic Corrosion Testing?
Depending on the type of exposure manufacturers want to test, CCT is conducted in a few different ways. In some cases, the material is submerged in water or corrosive materials.
In other tests, the material is put through a “dry off” process in an external environment. In others, materials may be sprayed or exposed in a CCT chamber.It’s not uncommon for CCT to be a somewhat complicated, multi-exposure process, wherein materials are subjected to different compounds one after another.
Why is CCT Popular in the Automotive Industry?
Modern cars are meant to perform well in virtually every situation, from pulling up outside the Roosevelt Hotel to splashing through mud, muck, and grime on springtime mountain roads. As such, the materials used to make modern vehicles need to be robust and durable.
Unfortunately, manufacturers can’t take every brand new car they produce and put it through a rugged road test to determine how the components will hold up to road salt and corrosive materials. This is where CCT comes in.
By providing a platform manufacturers can use to test automotive materials, without damaging the vehicles themselves, CCT allows manufacturers to outfit their automobiles with durable, road-ready materials that have been there and done that in the laboratory.
Which Automotive Components are Subject to CCT?
CCT is used to test a wide variety of automotive components.
In general, any component that will come into contact with corrosive substances, or is at risk of galvanic or crevice corrosion, will be tested in a CCT chamber. If a component proves vulnerable to a corrosive material, it will generally be coated with a material designed to prevent corrosion and keep the component intact.
This is where DECC steps in. We apply numerous corrosion resistant coatings, primarily zinc-flake in this instance, which have been tested and approved to a number of different OEM Cyclic Corrosion Testing standards.
For example, we spray Magni 565 on an almost daily basis. This zinc-flake coating system meets cyclic corrosion resistance standards for GM and Volvo, as well as SAEJ2334, which is a Society of Automotive Engineering (SAE) standard used all throughout the North American auto industry. We will cover zinc-flake coatings more in depth in next week’s blog post.
Today, customers want to purchase long-lasting vehicles, and CCT is one of the primary technologies that allows manufacturers to test their vehicles’ components before releasing them for sale.
If you need more information on how to find a coating that performs to a specific Cyclic Corrosion Testing standard, contact DECC today.
Related Articles
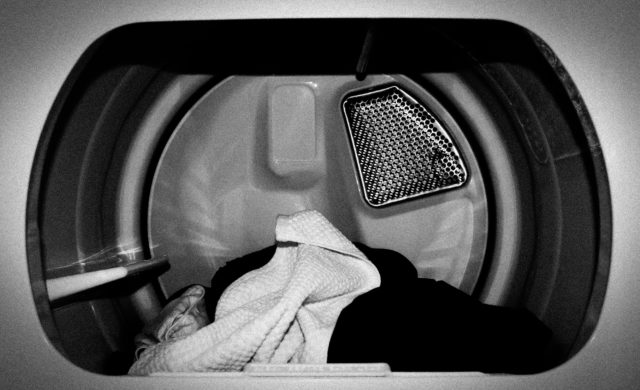
Reduce Plastic Sticking with Dryer Panel Coatings
DECC SOLVES PROBLEM OF PLASTIC STICKING TO DRYER PANELS
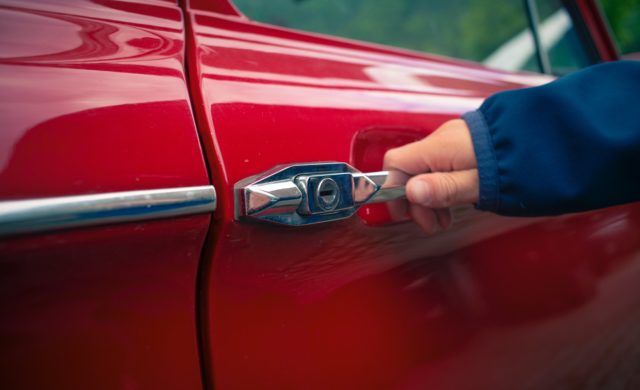
Coatings for a Quiet Ride
As cars have gotten quieter and quieter over the years, auto makers have...
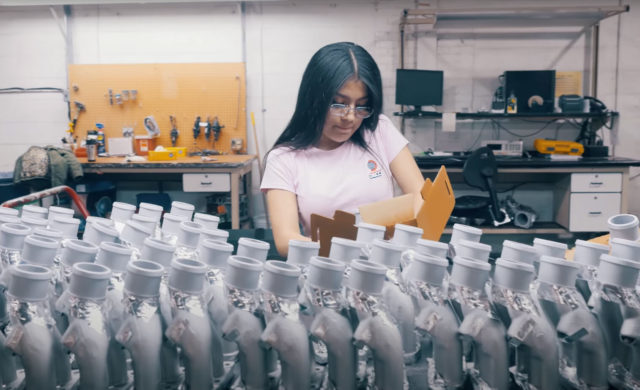
Dip Spin vs. Rack Spray – Why Not Both?
When it comes to the application of liquid-based functional coatings, there are two...