In every quality position, in every market, the goal is always the same: ensure the parts you are producing fall within their applicable measurements per the specification to guarantee a good part.
Almost all of these same quality professionals would argue that in an effort to limit your quality defects, you need to center your process variation, holding an agreed upon CPK.
However, some of the professionals that wouldn’t make that argument most likely work in the coating industry and have come to accept the fact that you cannot center your process with a liquid coating application. Explaining this to quality professionals that do not have experience dealing with coatings on a regular basis can be a tedious task, but it is a necessary one.
The Nature of the Beast
Coating industry-accepted measurement criteria is to take a specified number of measurements on various areas of a component and then average the readings. This average is then reported as the component’s coating thickness.
In this regard, if the coating thickness requirement is 10 to 15 microns, a thickness reading in one area that falls above or below the minimum or maximum requirement is not a cause for rejection as long as the average is within the specification.
There are many factors that contribute to the inability for any liquid coating applicator to center their process, ultimately the reason why thickness averages are industry accepted. The most prevalent are:
Customer Part Variation – because a coating applicator does not manufacture the component in which they are coating, they have no control of the variation in their customer’s process. Slight variations in the material thickness of the customer’s part can ultimately lead to amplified variations in coating thickness from an applicator’s standpoint when multiple measurement points are required.
Substrate Prep Variation – numerous coating resin systems require a mechanical prep to ensure proper adhesion, such as a blast process. Blasting a part creates microscopic peaks and valleys on a component (it does not impact the dimensional tolerance of a part). Because of these peaks and valleys, even if the coating was 100% uniform, you could measure thickness in two points that are a couple millimeters apart and get completely different readings.
Raw Coating Formulation – just as a metal stamper is allowed minor variation in their tolerances, so are coating manufacturers. Slight variations in solids content from lot to lot cause slight variations in coating thickness that cannot be anticipated, making it impossible to alter the process to compensate. Also, with coatings such as zinc-flake, the zinc-flakes must “lay down” on each other for the coating to provide corrosion protection (see picture below). Because of the way the coating is deposited on the part, you can see variations in thickness under a microscope that are, again, only millimeters apart.

Zinc Flake Coating Thickness Magnified
Faraday Cage Effect – in an electrostatic spray process, whether it be liquid or powder, charged coating particles are naturally attracted to leading edges of a component, preventing the coating from reaching recessed areas of a part. This ultimately requires a touch-up or secondary spray process to achieve complete coverage. As a result, the edges of a component will have a higher thickness reading than recessed areas. Both areas will be within the specification tolerance, but at complete opposite ends.
Because of the above, any coating applicator will not be able to achieve the goal of centering their process. It is just the nature of the beast that when given a tolerance range, a coating applicator will take up most of that range.
Fortunately for DECC, many of our top 15 customers have come to us when our competition has not been able to meet their required quality standards…so we like to believe we can control our process better than others.
If you are having coating issues with a current production part, or have a component with a challenging geometry for coating, contact us today.
Related Articles
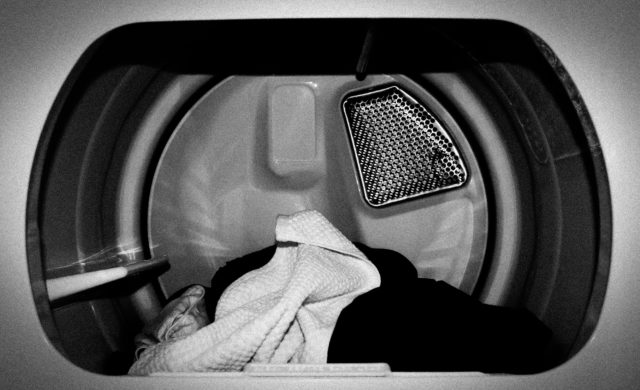
Reduce Plastic Sticking with Dryer Panel Coatings
DECC SOLVES PROBLEM OF PLASTIC STICKING TO DRYER PANELS
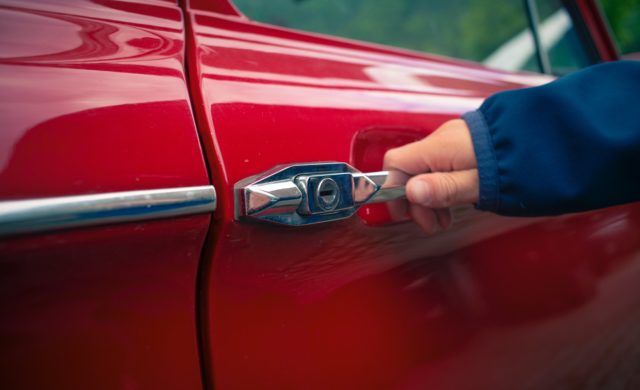
Coatings for a Quiet Ride
As cars have gotten quieter and quieter over the years, auto makers have...
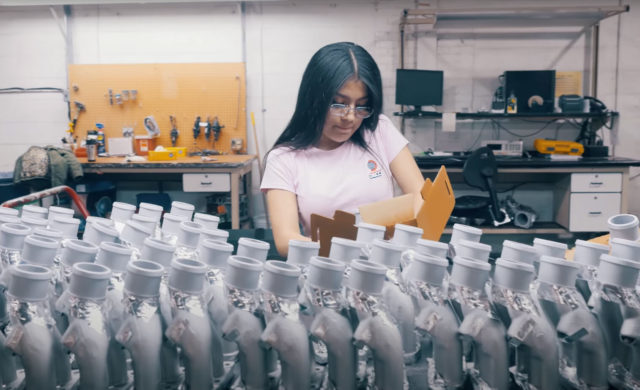
Dip Spin vs. Rack Spray – Why Not Both?
When it comes to the application of liquid-based functional coatings, there are two...