The DECC Company is an almost exclusively rack-spray facility. During the coating process, components never touch…they are all sprayed and cured on their own hook. The only time they touch is during the packing process, and that is only if the customer requires a bulk pack.
Dip-Spin vs Rack-Spray
What this means is that compared to a dip-spin, bulk application process, parts coated in a rack-spray process will have a much more uniform and quality finish. The necessity of 100% sorting is eliminated. However, the most important distinguishing factor is that fallout from the coating process is almost nothing where dip-spin can yield upwards of 20% defective parts each run.
Although pricing for a bulk, dip-spin process may be enticing on paper, the total processing cost for certain part geometries that don’t lend themselves to a bulk application tends to be higher than a rack-spray price.
Below is a video highlighting the technology we employ at DECC. If you are having quality issues with a dip-spin application, be sure to contact us to see if we can help.
Related Articles
Supply Chain Transparency
Leverage barcode scanning to capture location and other data at any number of...
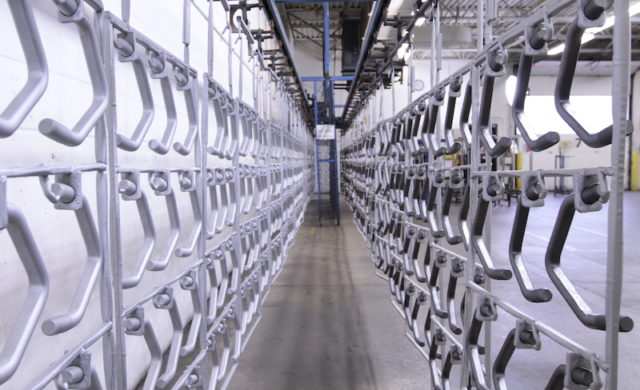
DECC Featured on Finishingandcoating.com
We were honored to be featured for an article on Finishingandcoating.com. Please be...
Thankful for the DECC Culture
A common thing said around DECC is that “anyone can throw coating at...