We have discussed in a previous blog post how DECC is “coating agnostic” and will often times provide samples with multiple coatings – from different manufacturers – for our customers to validate performance. Most often, if a dry-film lubricant is needed, a Xylan coating from Whitford is one of those options.
What is a Fluoropolymer Coating?
Whitford’s Xylan coatings are high-performance fluoropolymers. Fluoropolymer coatings contain low-friction, dry-lubricant materials suspended in a plastic binder. The plastic binder, which consists of a variety of organic polymers depending on the resin system, provides adhesion to the substrate and protection of the typically softer lubricating particles.
The most typical lubricant used in Xylan is PTFE (polytetrafluoroethylene) for multiple reasons: it has the lowest coefficient of friction of any fluoropolymer, it operates effectively at low and high temperatures, and is impervious to most chemicals.
Molydisulfide, graphite, FEP, and PFA are the lubricants prevalent in other Xylan variations, each providing unique performance characteristics that are geared toward specific applications.
The various combinations of binders and lubricants used in each resin system have allowed Whitford to produce more 3,000 Xylan formulations.
Because of all the variations, Xylan dry-film lubricants can solve a multitude of problems – from friction/wear and corrosion to non-stick release and noise reduction. What truly sets Whitford’s Xylan apart is its ability to operate in harsh environments, whether it be extreme temperatures or where a component comes in contact with a corrosive chemical…places where normal lubricants would cease to function.
Knowing the exact problem a customer is trying to solve allows DECC to make the appropriate Xylan recommendation.
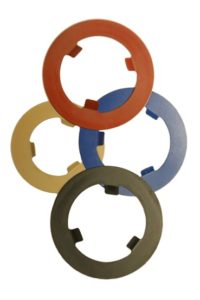
Automotive washers coated with various colors of Xylan 1014
DECC applies Xylan 1014 to automotive washers that go into wheel assemblies, Xylan 1010 to threaded rods that are used in hog farms, Xylan 1840 to plastic injection molds for release, Xylan 8870 to weld fixtures to prevent weld spatter from sticking….the variations of Xylan are as numerous as the end applications.
If you are experiencing a sticking, wear, noise, fretting, galling, corrosion, vibration or heat from friction issue…contact us today. If we can’t find a solution with a Xylan fluoropolymer coating (which we most likely can), there are other similar resin systems we can use to solve your problem.
Also, if you are looking for a more in-depth dive into Whitford’s Xylan coatings, as well as their other offerings, be sure to check out their Engineering Design Guide here.
Related Articles
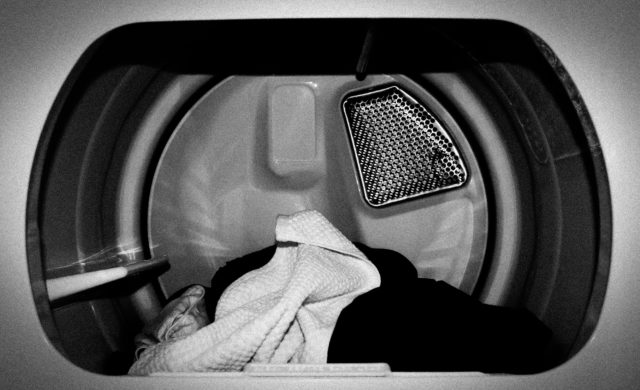
Reduce Plastic Sticking with Dryer Panel Coatings
DECC SOLVES PROBLEM OF PLASTIC STICKING TO DRYER PANELS
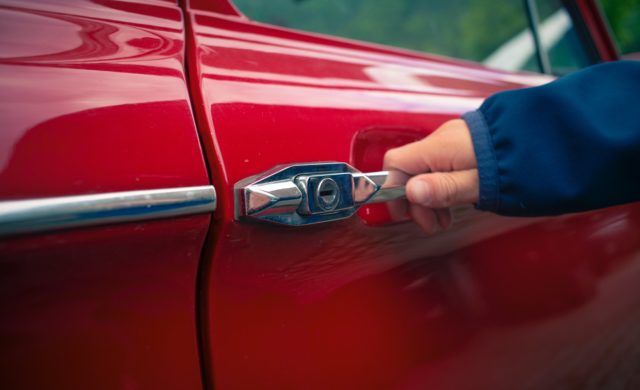
Coatings for a Quiet Ride
As cars have gotten quieter and quieter over the years, auto makers have...
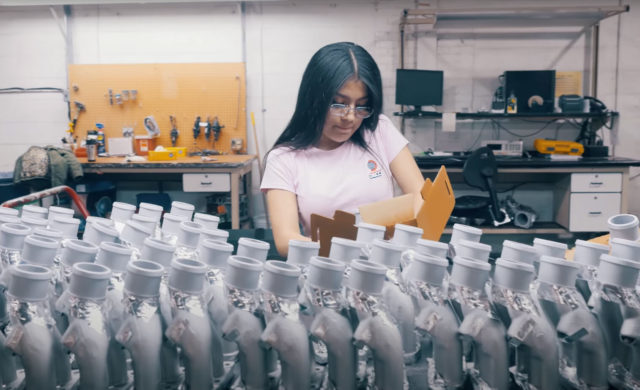
Dip Spin vs. Rack Spray – Why Not Both?
When it comes to the application of liquid-based functional coatings, there are two...