As there is a vast array dry film lubricants on the market, there are just as many different applications in which these coatings could be utilized.
Given the countless combinations of coatings and applications, determining which one would be best for your application can be a daunting task. However, by determining a few key variables, the options can be scaled down considerably.
When trying to decide which type of dry-film lubricant would be best for your application, the following should be considered:
- What is the substrate type – dry film lubricants cure at significantly varying temperatures, so selecting a coating that won’t detrimentally affect the substrate during the curing process can narrow your choices significantly. For example, Henkel’s Bonderite S-FN 310 (formerly known as Emralon 310) is two part PTFE lubricant that cures at 300° Henkel also produces a different resin-bonded PTFE lubricant called Bonderite S-FN 333 (formerly known as Emralon 333) that requires a minimum substrate temp of 600°F to properly cure. The 310 coating can be used on plastic or silicon substrates…the 333 coating, not so much.
- Does the part have plating – some components are plated for corrosion protection but require a functional dry film lubricant for other performance purposes. In the same vein as above, plating can begin to break down when exposed to temperatures in excess of 400°
- Does it need to be FDA acceptable – PTFE (polytetrafluoroethylene) is one of the main ingredients found in the coating on your non-stick pots and pans in your home. PTFE is also one of the main ingredients in the majority of dry film lubricants. Although PTFE itself is inert, the resin matrix that contains it may not be. If your application requires the coating to be FDA acceptable (to learn more about what that entails, click here), you must select a resin system that is graded as such. Whitford manufactures an extensive portfolio of FDA acceptable dry film lubricants.
- Does the part need elevated corrosion protection – almost all dry film lubricants offer some level of corrosion protection, but there are those that offer more than others. For example, Whitford’s Xylan coatings can last up to 2500hrs in salt-spray with less than 15% red rust when applied over a plated component. If a part is not plated, Molykote D-708 can achieve over 700hrs in salt-spray when applied over a phoshpated part. On the flip side, Molykote D-7409 is limited to 250hrs in salt-spray even though it is an excellent dry-film lubricant that is resistant to oil, grease, solvents, high temperatures and wear. The balance between functionality and corrosion protection for your application is a key determining factor when deciding on a resin system.
- What problem is the coating solving – is the component operating in a high load carrying capacity and there is sticking or galling? Is it interfacing with another component and causing noise? Does it sit idle for extended period of times so traditional lubricant isn’t an option? Or is it constantly cycling and traditional lubricant is breaking down? If you have the first four questions on this list determined, answering the last one will help to determine a resin system from the remaining coating choices.
To tie it together: let’s say I had a stainless steel component, so cure temperature is a non-issue. Because it is stainless, there is no plating. It does not need to be food grade. Because it is stainless, the corrosion protection is taken care of. This particular component oscillates inside an enclosed mating metal sleeve intermittently and under low load carrying capacity. The coating needs to prevent fretting and seizing of the action. The coating must last over a million cycles.
With all of that criteria, DECC would most likely suggest a moly-disulfide/graphite based lubricant such as Molykote D-7409. D-7409 is designed to be a permanent lubrication where oils and greases cannot be used. Also, because moly-disulfide is softer than other lubricants, the coating will “transfer” to the mating surface, which would be ideal in this type of enclosed application. This would ultimately create two lubricious surfaces and ensure the coating’s functional longevity.
If you have a component that will require a dry film lubricant, the above checklist should help narrow your choices. Or you can contact DECC and we can walk you thru the process.
Related Articles
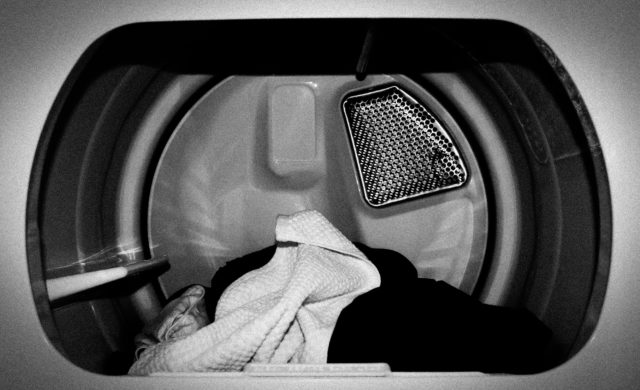
Reduce Plastic Sticking with Dryer Panel Coatings
DECC SOLVES PROBLEM OF PLASTIC STICKING TO DRYER PANELS
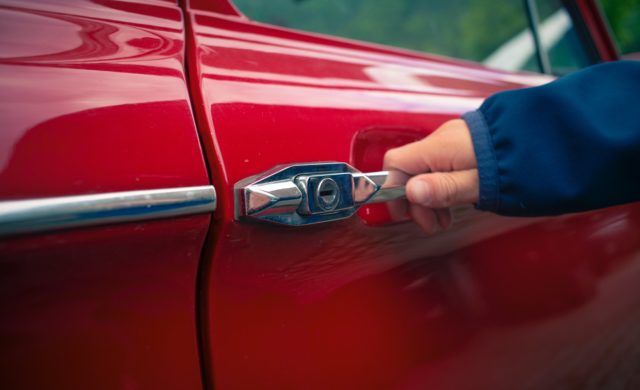
Coatings for a Quiet Ride
As cars have gotten quieter and quieter over the years, auto makers have...
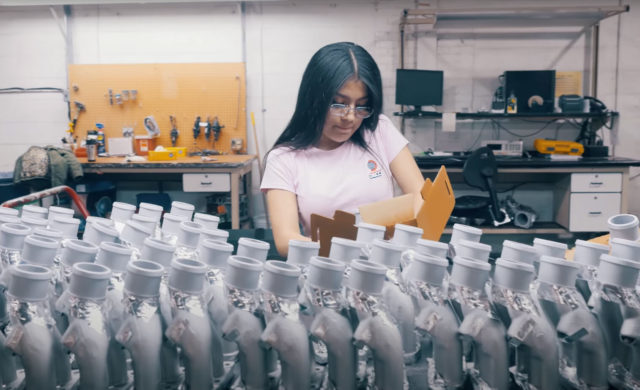
Dip Spin vs. Rack Spray – Why Not Both?
When it comes to the application of liquid-based functional coatings, there are two...