Producing quality product within a specified tolerance is a battle that every manufacturer, in every industry, fights every day.
Design engineers have the task of determining how tight of a tolerance should be allowed when developing a part and usually operate in the mind set of “the tighter the better.” In some cases, unnecessarily tight tolerances just drive up the cost of a component unnecessarily, but that is a debate for a different day.
It is understood that a component designed to need a functional coating would have its tolerances accordingly compensated. However, if the component you’re dealing with already has tight tolerances to begin with and a functional coating is determined to be a need after the fact, there should not be a stack up issue in the vast majority of instances.
For example, a typical “tight” tolerance is +/- 0.1mm. Converted to inches, this is about four thousandths of an inch, or .0039” (we will round up to .004” for simplicity’s sake).
In the coating industry, the most universal form of measuring a coating’s thickness is microns.
One thousandth of an inch is equal to 25.4 µm (microns). So four thousandths of an inch would be equal to 101.6 µm. Tighten the tolerance even further, let’s say +/- 0.05mm, and it would be 48.26 µm if you were to equate it to a coating thickness.
If it is assumed that the manufacturer of the component is not taking up the entire tolerance on the high side, a functional coating should not present any issues at all in terms of stack up, regardless of which type of coating you apply.
Fluoropolymer coatings, such as Whitford’s Xylan series, Henkel’s Emralon 333, or Chemours’ PTFE resins, provide dry film lubrication and non-stick release and are applied in film thicknesses of 15 to 25 microns in order to be functional.
Magni and Doerken zinc-flake coatings, which provide salt spray corrosion resistance in excess of 1000 to 1500hrs, are typically applied in thicknesses of 12 to 24 microns depending on the OEM specification.
Dow Corning’s Molykote D-708 anti-friction coating provides lubricity and corrosion protection in as little as 11 microns.
Although any coating applicator cannot center their process (read about that here), there should be enough “wiggle room” within the tolerance where coating peaks should not pose a problem. If coating thickness is extremely critical, a rack-spray process should be utilized.
If you have a component already in production and are in need of a functional coating, contact us today. As an exclusively rack-spray coating applicator, we can provide a consistent film build to ensure the part operates just as good, or better, than it was originally designed.
Contact UsRelated Articles
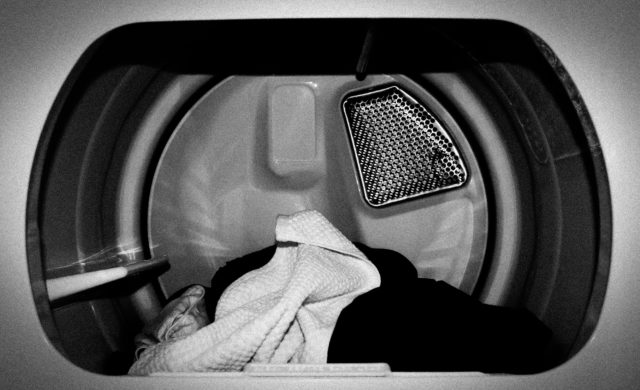
Reduce Plastic Sticking with Dryer Panel Coatings
DECC SOLVES PROBLEM OF PLASTIC STICKING TO DRYER PANELS
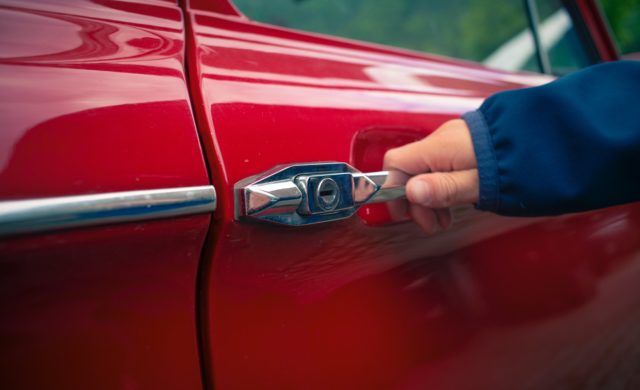
Coatings for a Quiet Ride
As cars have gotten quieter and quieter over the years, auto makers have...
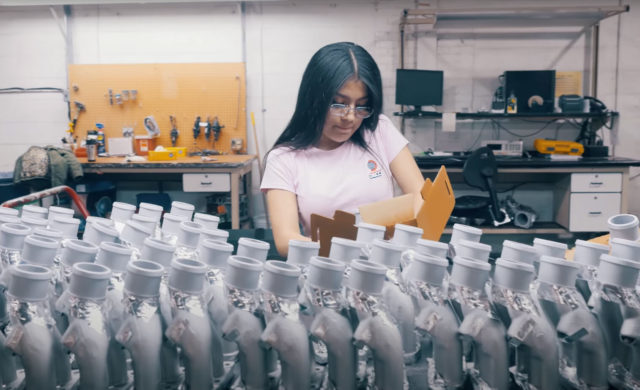
Dip Spin vs. Rack Spray – Why Not Both?
When it comes to the application of liquid-based functional coatings, there are two...