When needing a functional coating application, most components require complete coating coverage on the entirety of the part. When there are instances where this is not the case – such as cosmetic, fit or function implications – masking of certain areas of the part is necessary.
If an area of a part must be masked, there are a variety of options depending on component geometry, mask location and cure temp of the coating being applied.
Below are the five most typical types of masks used by coating applicators, particularly rack-spray applicators as almost all components requiring masking cannot be processed via a bulk application method.
- Silicone Plugs/Caps – capable of withstanding high cure temperatures – up to 600°F – silicone plugs and caps are the most prevalent masking materials in the coating industry. Ideal for masking holes, threads, and mating surfaces, they are long lasting, versatile and can be custom designed for use in almost any coating application. Caplugs offers a wide range of such products.
- Aluminum Tape – aluminum tape is beneficial for odd part geometries that require tight cut lines, essentially allowing you to make a “custom” mask in a pinch. However, applying the tape prior to coating is a rather tedious and lengthy process that can increase processing costs…albeit necessary. Although the aluminum tape can handle temperatures above 400 degrees, the adhesive cannot, ultimately limiting its use to coatings with lower cure temperatures.
- Cardboard – custom made cardboard masks are a perfect option for masking parts that do not require multiple coats so they can be removed prior to the curing step – such as a tray-spray application. Although this is where these types of masks are most widely used, there are instances when a multi-layer coating process does not require a full cure between coats. In such a case, the cardboard does not need to be removed in the final cure.
Valves with cardboard cutouts and silicone plugs for masking prior to coating
- 3D Printed Masks – maybe not the most utilized as of right now, 3D printed masks are quickly gaining popularity in the coating industry…whether they are done in-house or outsourced. While some custom silicon masks can take months to receive after an order is placed, 3D printed masks can be made in 24hrs or less. This allows applicators to begin development work on a potential job in an extremely short amount of time (which is why DECC purchased our own 3D printer).
- The Fixture – in the best case scenario, masking requirements can be built right into the fixture. While all of the above masks will work in their respective applications, they are an added step in the process where the mask must be applied before the parts can be placed on a hook or tray to be coated. If the mask can be built directly into the fixture, parts only need to be touched once before coating. Also, the costs of purchasing and replacing the masks are eliminated.
If you have a component that requires a functional coating, but only in select areas of the component, contact us today. Custom masking is one of DECC’s core competencies.
Related Articles
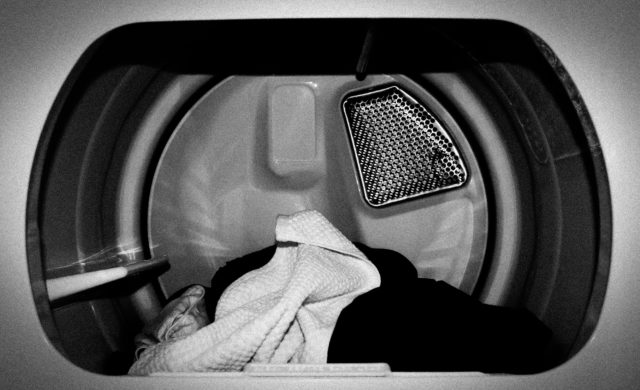
Reduce Plastic Sticking with Dryer Panel Coatings
DECC SOLVES PROBLEM OF PLASTIC STICKING TO DRYER PANELS
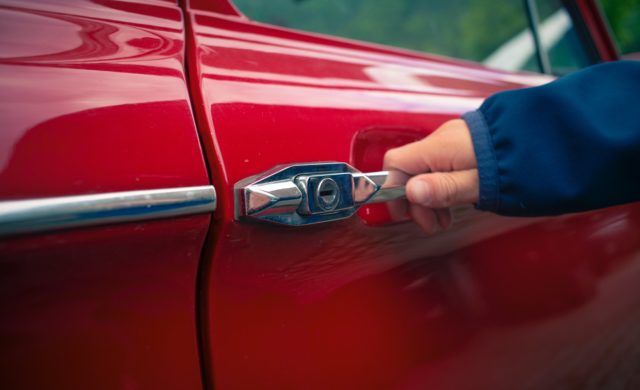
Coatings for a Quiet Ride
As cars have gotten quieter and quieter over the years, auto makers have...
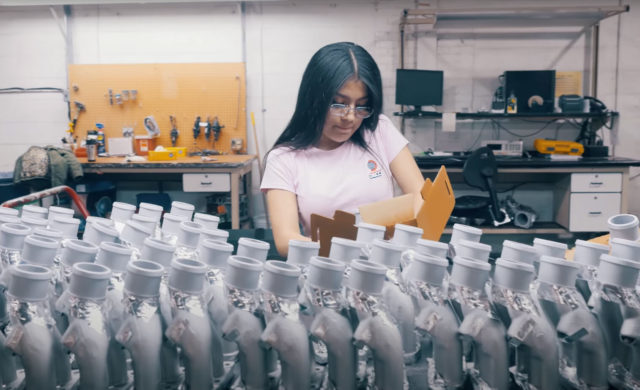
Dip Spin vs. Rack Spray – Why Not Both?
When it comes to the application of liquid-based functional coatings, there are two...