We have had customers contact us because coated parts being received from their current coating applicator were "underperforming."
In almost all of the instances, we determined that the coating was not cured properly. It was uniformly applied and appeared functional, but subsequent quality checks (such as an adhesion or solvent wipe) determined this was not the case.
In our last blog, we discussed the criteria of what makes a coating functional, which is when a coating has performance characteristics that go above and beyond being just decorative or protective. In order for a coating to perform at is highest intended level, it must be processed to ensure it exhibits full film properties.
Coating manufacturers design coatings to do some pretty amazing things when you consider how thin they are applied (typically a mil or less for the coatings DECC sprays). However, if they are not applied and processed in accordance with the PDS (Product Data Sheet), the manufacturer will not guarantee performance. Probably the most important step to guarantee a coating’s performance is to ensure the proper bake time and temperatures have been achieved during cure.
The temperature in this instance refers to substrate temperature, not oven temperature. For a coating to achieve the proper bond to the substrate to which it is applied, the substrate must hit the required temperature called out on the PDS. However, this is where it can get tricky and bake time is critically important.
A thin piece of material will heat up much quicker than a thick piece of metal, so small components can spend much less time in an oven than larger ones, even if the same coating is applied to both. This is why some larger components are off-line baked in batch ovens because of the dwell time required to get the substrate to temperature. Thermal couples are also often used on thick, heavy pieces to ensure they reach temperature.
Some coatings can be under-cured and still provide functionality. This is done only if a substrate cannot handle a coating’s final cure temperature (for example, if a part is plated). However, it will not perform to its highest capability. Only once the proper cure cycle has been completed will the coating then exhibit its full film properties and provide the functionality the manufacturer intended.
Be sure to reach out to us. We have found that our systems are more robust than others, providing accountability to our customers and ensuring they receive a quality product every time.
Contact UsRelated Articles
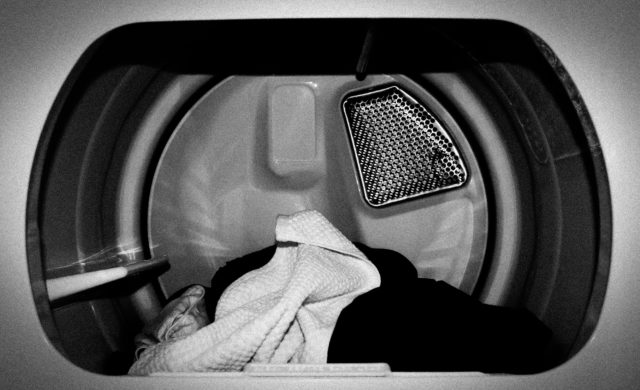
Reduce Plastic Sticking with Dryer Panel Coatings
DECC SOLVES PROBLEM OF PLASTIC STICKING TO DRYER PANELS
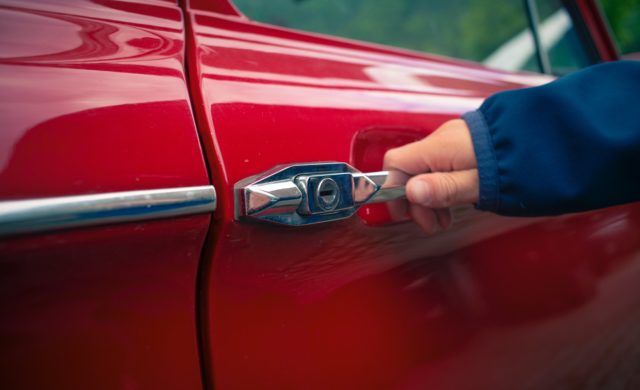
Coatings for a Quiet Ride
As cars have gotten quieter and quieter over the years, auto makers have...
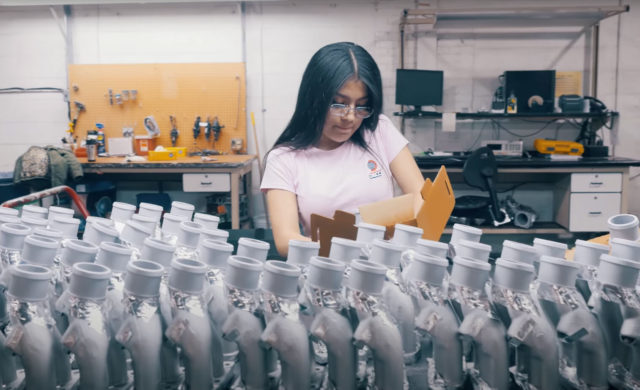
Dip Spin vs. Rack Spray – Why Not Both?
When it comes to the application of liquid-based functional coatings, there are two...