When a customer asks our team, “How much will this coating application cost?” there are many factors we consider—and the size of a component is just one of them.
Let’s dive into the hidden costs of smaller volumes, and some of the ways we find cost efficiencies, so you can get more strategic about the schedules you plan and the coatings you choose.
In Case You Didn’t Know…
DECC is almost an exclusively rack-spray coating company. This method involves hanging or placing a part on a fixture and then spraying the coating utilizing either electrostatic guns, HVLP guns, or a combination of both. Both types of guns could be either automated or used by a hand-spray technician.
Why Changeover Matters
On the spray line at DECC, changing coatings is one of biggest places we gain or lose time. As skilled as our line operators and engineers can be, it typically takes 10-15 minutes to load in a new coating.
Picture our line as a train track and the products we’re spraying as the train coming down those tracks. After the caboose of one product, we intentionally place a long gap. The line continues moving, but this gap allows our team to do a flush-out of the current coating so that we can prepare the spray guns for the next coating needed.
The next product in line will have the same solvent base as the last. But if not, we have to flush with a solvent two times—because some coatings just aren’t compatible with each other. High temperature resistant coatings, rubber bonding adhesives, corrosion protective coatings, and other coatings all have properties that can’t mix with others, otherwise things can go wrong.
Same Coatings = More Efficiency
As you might guess, our most efficient jobs are large-volume jobs where the line keeps moving, products keep coming, and changeover isn’t required. When this happens, our customers save money.
But high volume doesn’t have to mean spraying a single component. You could have a high volume spread across five different parts, all needing the same coating. As long as they require the same coating, no changeover is needed, and you’ll see the savings.
It really depends on your unique needs but think of it this way: If you have two products that need two different coatings, it will always require a changeover. But if you can alter your schedule so that all the products you need require the same coating, you’ll see cost savings on the estimate we provide.
The takeaway: When you want to save on costs, don’t just look at the quality of a coating. Consider the volume you’re ordering and how ordering components needing the same coating can influence your estimate—and ultimately your bottom line.
Related Articles
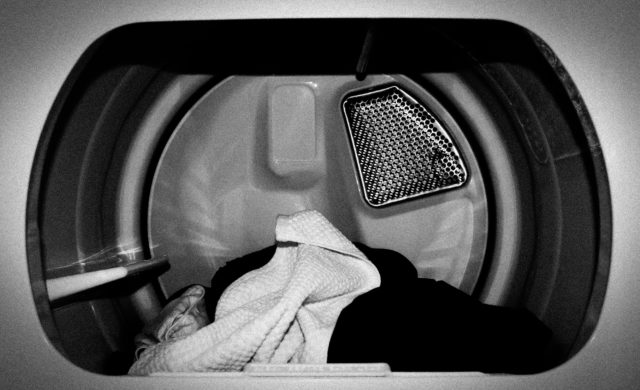
Reduce Plastic Sticking with Dryer Panel Coatings
DECC SOLVES PROBLEM OF PLASTIC STICKING TO DRYER PANELS
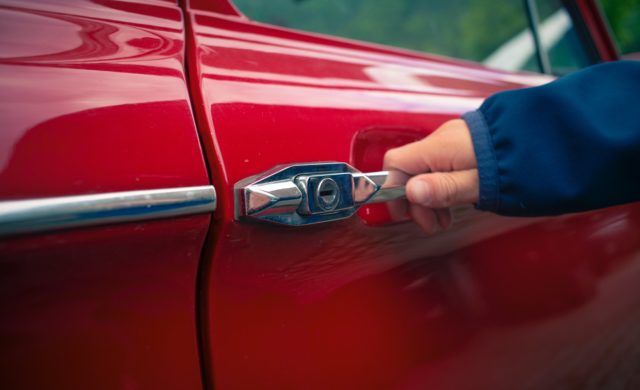
Coatings for a Quiet Ride
As cars have gotten quieter and quieter over the years, auto makers have...
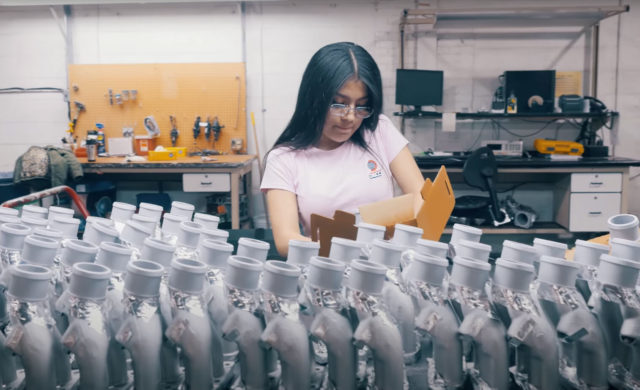
Dip Spin vs. Rack Spray – Why Not Both?
When it comes to the application of liquid-based functional coatings, there are two...