Utilizing a rack-spray coating application for your components as opposed to a dip-spin method has many obvious benefits.
Among those are a much more consistent and quality finish, less fallout due to damaged parts, and less rework or sorting due to coating defects.
However, one overlooked benefit of a rack-spray versus a dip-spin process is usually not realized by our customers until the first time we call to tell them they have an issue in their process and we have received defective parts.
Because of the very nature of a rack-spray application, every part we process has to be touched, picked up, looked at and hung on a fixture. During this process, we sometimes find our customer’s defects that they didn’t even know they had.
As a result, we offer our customer a line of defense in preventing potential quality defects that were created in their manufacturing process – not our coating process – from reaching the end customer.
It should be noted that usually when we find defective parts, they are not the result of a widespread process failure at our customer. Often times we find a dozen or so defective parts out of a lot of 100,000 pieces if, for instance, a slug from a stamping got stuck in a die and produced some parts that would be rejected at their end customer…or if a weld nut happened to be missed during processing.
In a dip-spin application, these would pass thru the coating process and if there was not a 100% sort afterward would ship right to the end customer, ultimately resulting in a rejection and a corrective action.
The actual fixturing of a component on a coating window could bring to light a defective part as well. For instance, the parts below require a fixture with a tight tolerance to ensure they do not fall off during processing. In the past, we have received oversized parts from our customer to the point they would not fit fall off the fixture. This allowed us to alert our customer they had a batch of components outside of their process parameters, ultimately saving them from a huge issue with their end customer.

Office Chair Tubes Prior to Coating
However, the fact that a rack-spray process allows for this type of oversight adds a tremendous amount of additional value to the service DECC provides. If you are experiencing any quality issues with your current coating application and would like us to take a look, do not hesitate to contact us.
Contact UsRelated Articles
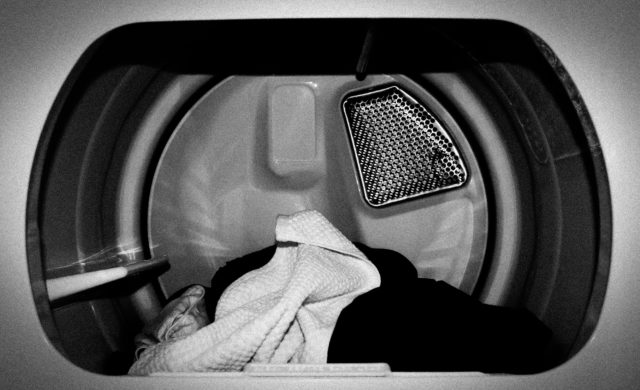
Reduce Plastic Sticking with Dryer Panel Coatings
DECC SOLVES PROBLEM OF PLASTIC STICKING TO DRYER PANELS
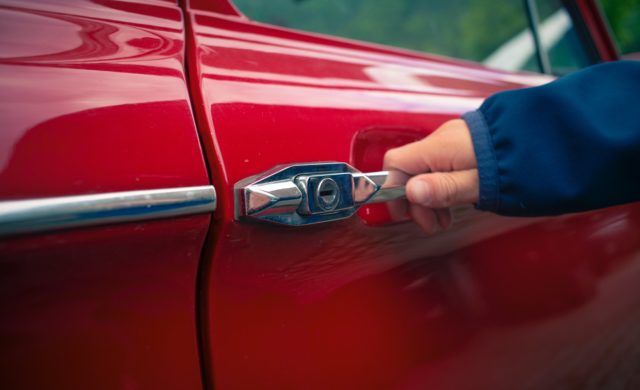
Coatings for a Quiet Ride
As cars have gotten quieter and quieter over the years, auto makers have...
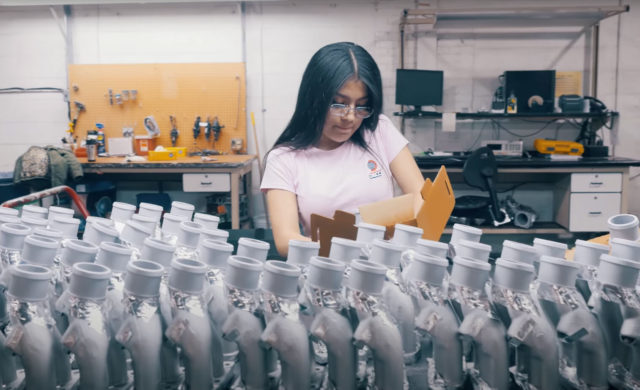
Dip Spin vs. Rack Spray – Why Not Both?
When it comes to the application of liquid-based functional coatings, there are two...