A good amount of commercial food grade processing equipment comes “out of the box” with non-stick, FDA acceptable coatings applied to the appropriate machine mechanisms (learn why we say “FDA acceptable” and not “FDA approved” here).
As is with all new purchases, everything works great for a period of time. However, food ingredients can be surprisingly abrasive or acidic and coatings are not impermeable to wear, even the most robust ones.
Conversely, when the equipment does not come with a coating and sticking ingredients start impeding production for extended periods of time for cleaning, it is determined only after processing that one is needed.
In both instances, it is probably more cost effective to contact a local coating applicator to apply an FDA acceptable coating than it would be to contact the manufacturer for a replacement component or to have them locate an applicator.
However, it should be noted that there is no one cookie cutter FDA acceptable coating (no pun intended) that can solve every issue.
For instance, do you need non-stick release AND abrasion resistance or just the release properties? An example would be a coating for a cereal conveyor belt vs a bread roller machine, both challenging issues we have been able to solve for customers.
In the case of the cereal conveyor belt, the sticky cereal that was going through a drying process was adhering to and plugging the holes in the conveyor. A highly non-stick surface was needed while abrasion resistance was of little concern. Because the top coat is focused solely on release, DECC applied the Whitford Eclipse two-coat system and eliminated the issue. The coating prevented most of the sticky buildup and dramatically decreased cleaning times when required.

Cereal conveyor with an FDA acceptable coated slab next to uncoated slabs
In the case of the bread roller, the dough is rolled in a higher load capacity…and the dough is both sticky and abrasive. Both abrasion resistance and non-stick properties were essential. We originally applied the Eclipse system as well, but the pressure and abrasiveness of the dough proved too much.
We decided to try Xylan 8870 from Whitford, which is built with abrasion resistance and non-stick release in a single coat. This coating choice was successful and helps to reinforce that each application is unique and may require a unique coating.
If you are contacting a coating applicator to refurbish your used equipment or to suggest an FDA acceptable coating for a previously uncoated component, make sure they ask questions regarding the environment the part operates in, the ingredients being processed, and what your expectation of the coating would be.
If they do not ask these questions before suggesting a coating choice, contact another applicator…or give us a call. We know from experience that there is no magic bullet coating…which is why there are so many FDA acceptable coating options. Knowing which one to choose can be difficult, which is why we are here to help.
Related Articles
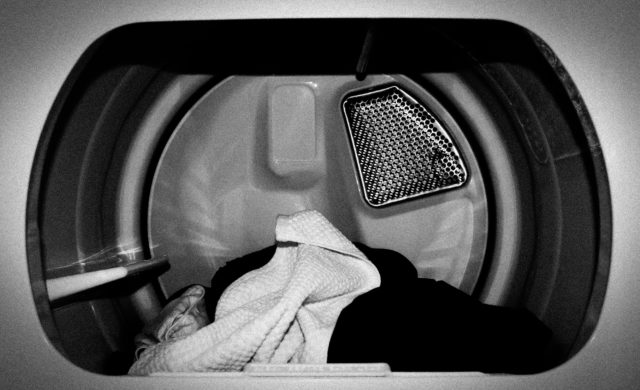
Reduce Plastic Sticking with Dryer Panel Coatings
DECC SOLVES PROBLEM OF PLASTIC STICKING TO DRYER PANELS
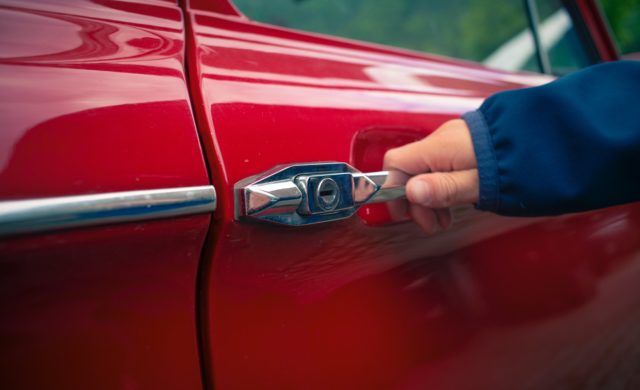
Coatings for a Quiet Ride
As cars have gotten quieter and quieter over the years, auto makers have...
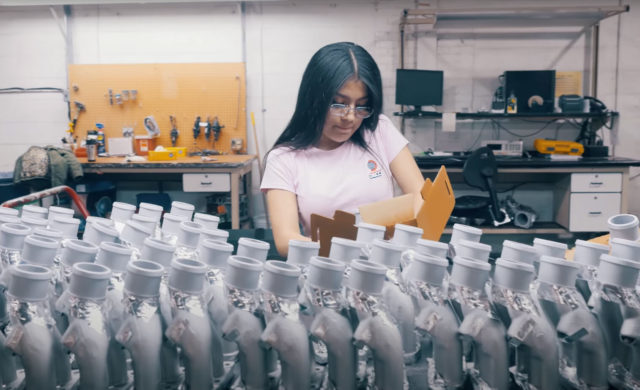
Dip Spin vs. Rack Spray – Why Not Both?
When it comes to the application of liquid-based functional coatings, there are two...