As an exclusively rack-spray applicator, DECC utilizes two types of spray guns to apply coating to our customer’s parts.
Due to EPA regulations, we are not allowed to use conventional spray guns so we use HVLP and electrostatic spray guns. Both have their pros and cons but are extremely effective in providing complete coating coverage, with limited waste, when used on the proper part geometries.
HVLP Spray
HVLP stands for High Volume Low Pressure. A spray gun works by introducing compressed air to a stream of coating. The compressed air breaks up the coating into smaller particles. The High Volume of air allows for the coating particles to be broken up even smaller than a conventional spray gun that has high pressure, but not necessarily the amount of air volume. The Low Pressure slows the forward velocity of the coating particles so that they don’t blow past or deflect off of the spray target.
If you can imagine spraying a water hose at a wall, the water will hit the wall and go in a 360 pattern around the main stream. The lower pressure pattern allows for more control and puts more coating on the part and less waste in the filters.
Electrostatic Spray
Electrostatic spray is where the coating is delivered through a charging zone or field where negatively charged ions are passed to the coating particles. The negatively charged ions cause the coating particles to separate, similar to how two magnets push apart when their negative sides are facing one another. These negatively charged coating particles leave the gun in a very fine mist and are now “looking” for a ground, which in this instance would be the grounded part on a hook. This separation also allows for lower atomization settings, which equals less forward velocity, and ultimately superior transfer efficiency with even less waste than an HVLP gun.
Electrostatics can be used with a spray gun or rotary bell
The atomizing of the coating in an electrostatic spray gun is the same as an HVLP spray gun, but the difference is you now have an electrical field at the end of the gun introducing those negative ions to the coating particles, which vastly improves coating wrap and transfer efficiency.
For the best application, an electrostatic rotary bell is the optimum choice for charging a coating. Coating is delivered through a rotating cup that has multiple holes and serrations on the ends. The cylinder or cups rotate at a speed of 40,000 to 60,000 rpms. The coating is delivered at a low flow through the rotating heads, breaking coating particles up, and giving the ultimate atomization. There is minimal forward velocity, which gives plenty of time for the coating to be attracted to the grounded part passing in front of it.
Limitations
Using an electrostatic bell is great for parts that are flat with minimum depth and angles. But when parts have aggressive angles and deep pockets, it becomes difficult to get complete coverage in those areas due to the Faraday cage effect.
Because the coating particles are charged, the coating will build up at the leading edges of the pockets and not in the deep recesses. This can be improved by both reducing the KV (charging of the coating) and increasing the shaping air. However, this will increase forward velocity, ultimately negatively impacting transfer efficiency.

DECC’s robots applying a touch-up coat with an electrostatic HVLP gun
Best Recipe for Success
For optimum results, a combination of a rotary bell and electrostatic HVLP spray gun can be utilized. This is the method DECC employs – we have electrostatic rotary bells and then the parts pass by two robots for touch-up purposes. The rotary bell can take care of 90% of the part while the electrostatic spray gun takes care of the other 10%, depending on part geometry. The electrostatic spray gun has the ability to still charge a little but also gives the coating more forward velocity to get into the hard to reach areas. This method ensures complete coating coverage on even the toughest part geometries.
Give DECC a call to see if we can help with a customized solution for your coated production part.
Contact UsRelated Articles
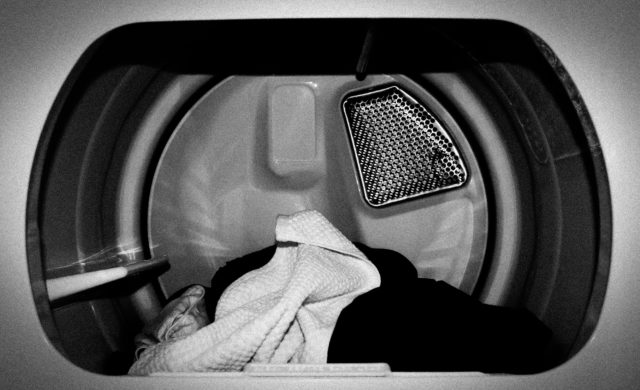
Reduce Plastic Sticking with Dryer Panel Coatings
DECC SOLVES PROBLEM OF PLASTIC STICKING TO DRYER PANELS
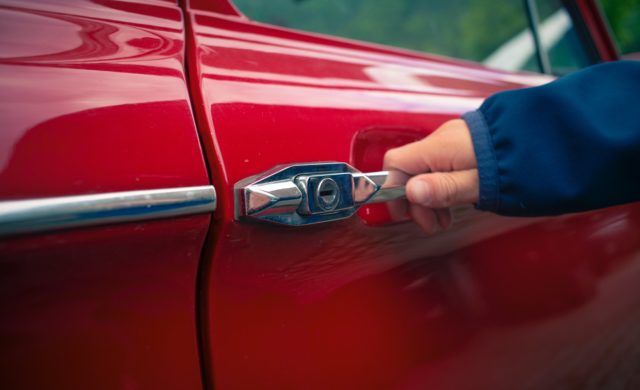
Coatings for a Quiet Ride
As cars have gotten quieter and quieter over the years, auto makers have...
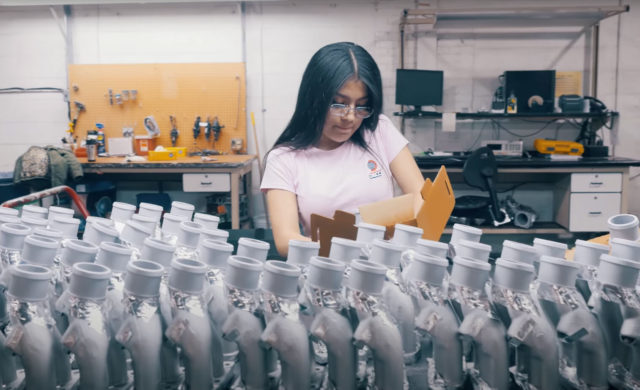
Dip Spin vs. Rack Spray – Why Not Both?
When it comes to the application of liquid-based functional coatings, there are two...