When you hear the term “non-stick”, most people immediately have their favorite cooking skillet pop in their head.
While this is true – non-stick pans are non-stick because most are coated with a PTFE coating – the applications of the aforementioned coating are far more reaching than just kitchen products.
Below are various instances in the automotive and manufacturing sectors where the application of a non-stick coating solved – or vastly improved – a component performance, machine performance, or excessive downtime related challenge.
Automotive
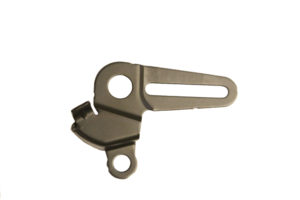
A latch component with a non-stick coating applied
A major OEM was having issues with the latch mechanisms on the rear liftgate of their newest truck model during cold cycle testing. Condensation and water would freeze on the plated components, ultimately preventing the liftgate from functioning. We applied Henkel’s GP 1904, a PTFE and graphite based coating with a low cure temperature so the plating would not be impacted. This non-stick release coating prevented the ice from adhering to the component, allowing the liftgate to operate in the cold with no issues.
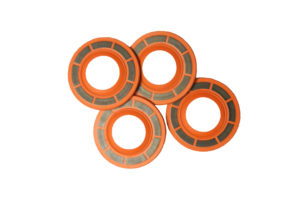
A silicone poppet seal with a non-stick PTFE coating
In another instance, a Tier I automotive supplier was experiencing failures in their emission system sensor assembly due to a silicone poppet – the silicon rubber was sticky and attracted contaminates that caused an ineffective sealing surface. We applied Henkel’s two-part, phenolic resin-bonded PTFE coating Emralon 310 (now called Bonderite S-FN 310). This low cure coating prevented dust and contaminants from sticking to the silicon sealing surface, ultimately resolving their failure mode.
Manufacturing
A furniture producer was experiencing excessive downtime due to the length of time it took to clean the glue off of the fixtures, blades, and machine components they used in their seating and table manufacturing area. We applied Henkel’s Emralon 333 (now called Bonderite S-FN 333) and its non-stick release qualities significantly reduced the time it took to remove the glue.
Numerous high-volume metal fabrication companies contact us to see if there is a more robust solution to prevent weld spatter from sticking to their fixtures other than spraying it every other cycle with a silicon aerosol. In these instances, we apply Whitford’s Xylan 8870 – a non-stick release coating that is also high-temperature resistant – allowing weld spatter to be simply brushed off.
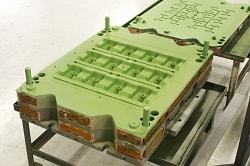
Plastic injection mold with Xylan 1840
A large rubber injection molding company was looking for a durable coating that not only aided in the release of their components from the mold after processing but also expedited routine cleaning. We applied Whitford’s Xylan 1840 – what they claim to be their best non-stick coating matrix – and solved both of their challenges.
Even if your situation is not exactly the same, perhaps some similarities in the aforementioned examples have led you to believe a non-stick coating application could be a solution to a problem you are facing. If so, contact us and we can recommend a resin system that we think can help with your unique challenge.
Contact UsRelated Articles
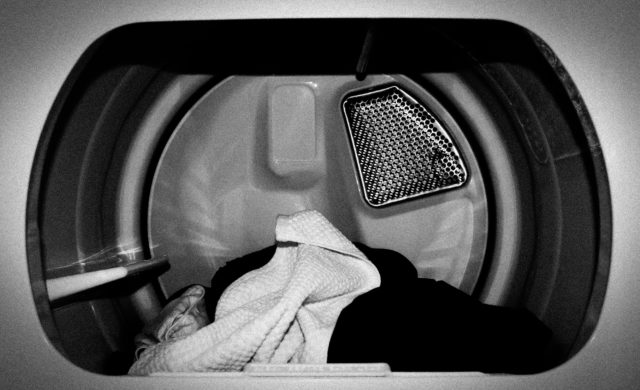
Reduce Plastic Sticking with Dryer Panel Coatings
DECC SOLVES PROBLEM OF PLASTIC STICKING TO DRYER PANELS
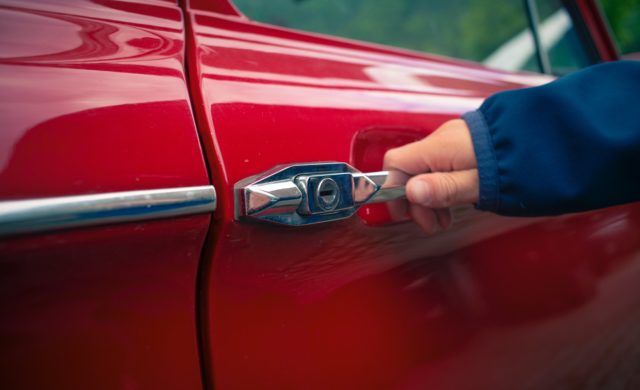
Coatings for a Quiet Ride
As cars have gotten quieter and quieter over the years, auto makers have...
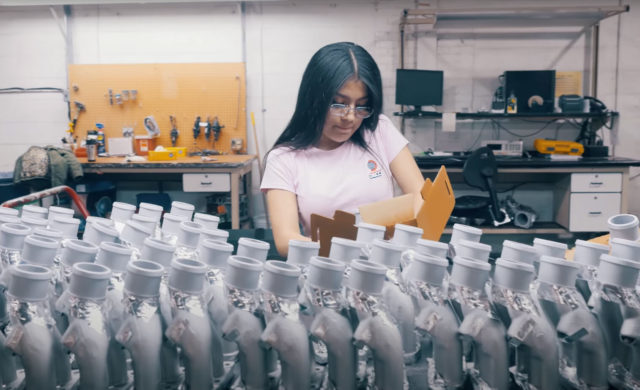
Dip Spin vs. Rack Spray – Why Not Both?
When it comes to the application of liquid-based functional coatings, there are two...