Abrasion is the grinding, wearing, or rubbing away by means of friction. In almost any industry, abrasion is one of the main causes of premature component failure.
Regardless of how smooth the finish appears to be, there are microscopic peaks on any substrate’s surface. When actuating or moving against a mating metal part, these peaks can momentarily weld together, tear off, and leave pits on the surface.
When not addressed, this mechanical action is what causes the wearing and degradation of a component, contributing to reduced part performance and premature failure.
However, the application of an abrasion-resistant coating to one or both mating surfaces can prevent these peaks from making contact with each other, ultimately reducing excessive friction and wear while improving part performance and ultimately extending a component’s functional life cycle.
What is an Abrasion Resistant Coating?
An abrasion resistant coating is essentially a dry-film lubricant. However, as there is a myriad of dry-film lubricants on the market, certain dry-film lubricant resin systems offer extended abrasion and wear resistance because of their formulation.
So as opposed to referring to them solely as a dry-film lubricant, DECC refers to those that offer a more robust chemical makeup and provide increased levels of wear resistance as abrasion resistant coatings.
Types of Abrasion Resistant Coatings
Abrasion resistant coatings, as mentioned, typically employ more than just a single lubrication system or a more robust resin bonding system. This dual attack on reducing friction is what increases their abrasion and wear resistance.
For example, Whitford’s extensive Xylan series of high-performance fluoropolymer coatings use a variety of formulations to increase abrasion and wear resistance.
Xylan 1052 is ideal for high-pressure, low-speed wear applications that are also subjected to extreme pressures of up to 150,000 psi. Instead of utilizing solely PTFE for lubrication, the coating also contains molydisulfide which helps to reduce cold-flow distortion that plague purely PTFE based coatings, ensuring coating performance longevity and increased wear and abrasion resistance…even in tough chemical environments.
Similarly, Xylan 1054 uses a combination molydisulfide and graphite as its lubricants. This coating is ideal for long-term lubrication and wear resistance when the non-stick release and chemical resistance properties of PTFE are not required.
However, Xylan 1014 contains only PTFE as its lubrication system but also contains significantly more bonding resin. This modified formula produces a harder, less porous and more abrasion resistant coating than its counterparts with a more even distribution of lubricant and resin binder.
Another coating formulation successful against abrasion is a combination of PTFE and FEP (fluorinated Ethylene Propylene), such as Henkel’s Bonderite S-FN 333 (formally called Emralon 333). FEP is very similar in composition to PTFE but is softer and more abrasion resistant, essentially amplifying the wear resistant qualities of both components. For instance, the below brake clips lasted over 2 million testing cycles without failure after being coated with Emralon 333.

Brake Clips Coated with Henkel’s Bonderite S-FN 333, Formerly Emralon 333
Choosing the Right Abrasion Resistant Coating
There are many things to contemplate when choosing which abrasion resistant coating is ideal for your particular application. However, you typically need to consider the environment that the component operates in to begin narrowing your choices.
For example, what is the continuous operating temperature this component will see? Is it exposed to chemicals or the atmosphere? Does the surface experience high-pressure or low-pressure load characteristics? For instance, some coatings exhibit greater wear resistance characteristics but provide limited corrosion resistance, be it chemical or atmospheric.
By addressing those variables, the question of which coating is ideal will become more clear.
If you require input as to which coating choice you should consider, contact us today. We typically will provide you with multiple options to trial and determine which is the best fit for your part performance challenge. And if we can’t solve your problem, we will try to help you find someone that can.
Related Articles
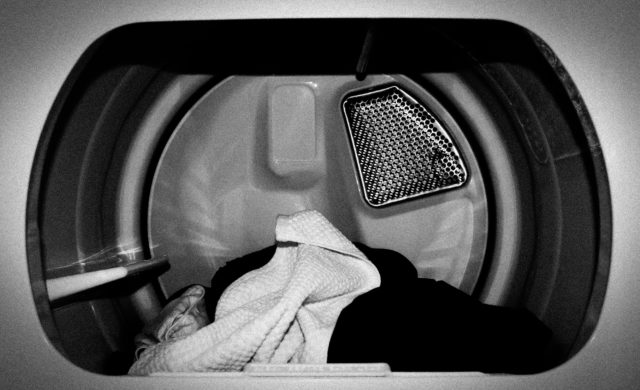
Reduce Plastic Sticking with Dryer Panel Coatings
DECC SOLVES PROBLEM OF PLASTIC STICKING TO DRYER PANELS
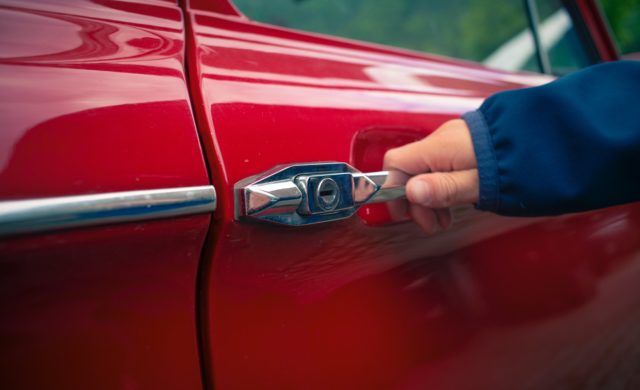
Coatings for a Quiet Ride
As cars have gotten quieter and quieter over the years, auto makers have...
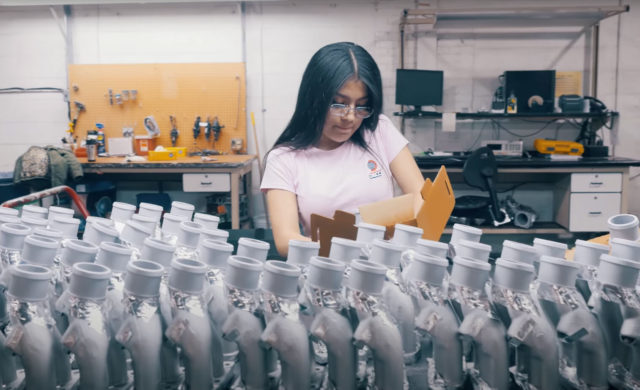
Dip Spin vs. Rack Spray – Why Not Both?
When it comes to the application of liquid-based functional coatings, there are two...