Hand spraying is a skilled trade that is becoming obsolete due to advances in technology. Most notably, robotics have taken over a large portion of spray applications from their human counterparts in the liquid coatings industry.
As the technology becomes more and more popular, the need for a skilled human becomes less and less. However, regardless of advances in technology, there will still be a need for hand sprayers in liquid coating applications for a few different reasons.
The Benefit of Hand Sprayers
The most prevalent reason is versatility: a human can jump in a booth and spray parts with different part geometries on a whim, especially if they are an experienced hand sprayer. While a robot will provide a more repeatable application because it does not experience fatigue, it still must be programmed first. Programming a robot is a task in and of itself and is generally a time-consuming process.
In the same vein, programming a robot is a lengthy process because it lacks the instant feedback a human can provide. A skilled hand sprayer can provide instant feedback at the point of delivery and make immediate adjustments where a robot cannot.
Lastly, a high-end, fully integrated, programmable robot can cost upwards of $50,000. This is assuming the infrastructure where the robot is housed is in place, as well. An investment into an individual that can program the robot (or an investment into training an individual) will be required, as well as additional costs of machine upkeep and critical parts inventory. Some companies cannot afford an up-front investment such as this and employing a skilled hand-sprayer mitigates that cost while also providing the aforementioned flexibility.
Training the Next Generation of Hand Sprayers
Although some may think that hand spraying is easy and anyone can just pick up a gun and have at it, which is far from the case.
A skilled hand sprayer has endurance and flexibility along with smooth and fluid movements. To watch an experienced person hand spraying on a moving conveyor line is akin to watching a dance performance: steps are and spray patterns are smoothly repeated over and over with precision. Just like learning a choreographed dance, hours upon hours of practice is required to perform on such a level.
This “practice time” is why finding new hand sprayers is becoming increasingly difficult. Because there are fewer of them employed within a company, devoting their time to training employees as opposed to spraying production can stretch resources thin.
Also, the best way to learn the trade is by doing – as in spraying actual parts. This can prove difficult because learning on current parts can delay delivery or pose a risk of quality defects. And practicing on a limited amount of defective parts does not provide the operator the chance to mimic a lengthy production run.
Because of the above, DECC has recently investigated virtual reality spray training from a company called SimSpray. Trainees are immersed in a virtual 3D environment and learn proper equipment setup, gun movements and body positioning on customizable projects. This type of training does not require the experienced sprayers to be present and allows employees to train for hours upon hours without interrupting production schedules, potentially causing quality defects on customer components, and without the need for a copious amount of scrap parts to practice on. While somewhat costly, it is far less than a robot and will ensure quicker, safer and more cost effective training of the next generation of hand sprayers.
DECC currently employs several hand sprayers (and managers/engineers) that have well over 100 years of combined experience in the trade. If you have a coating challenge that requires a “personal touch,” contact us today.
Related Articles
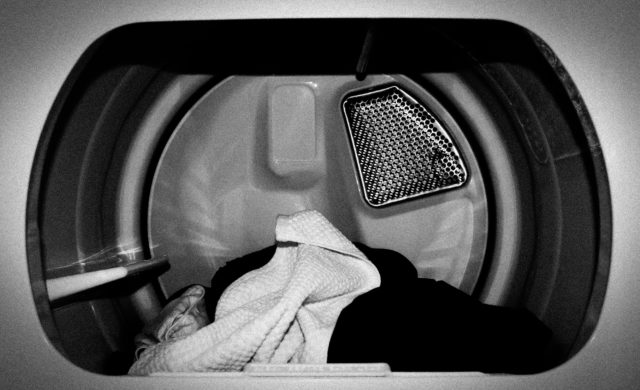
Reduce Plastic Sticking with Dryer Panel Coatings
DECC SOLVES PROBLEM OF PLASTIC STICKING TO DRYER PANELS
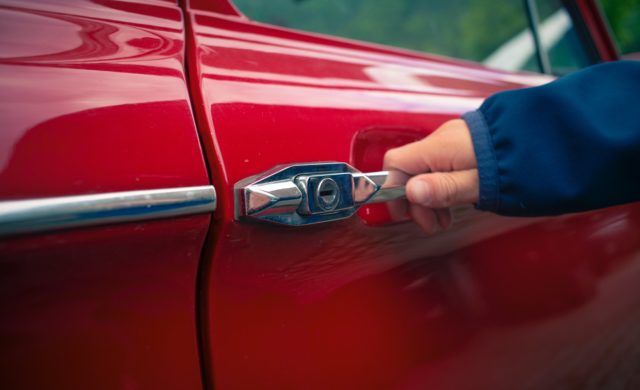
Coatings for a Quiet Ride
As cars have gotten quieter and quieter over the years, auto makers have...
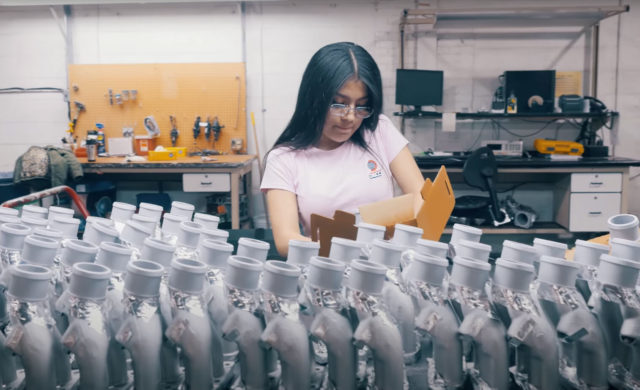
Dip Spin vs. Rack Spray – Why Not Both?
When it comes to the application of liquid-based functional coatings, there are two...